Customer/Social Needs Assessment and Innovation Management
We creates roadmaps based on the market of 10 years into the future. With our philosophy of taking the lead in developing the products that customers seek, we have created a research and development system for products and solutions. In creating our roadmaps, we gather feedback from outside experts and customers and work together to develop products which fit the future plans of our customers. We also regularly review and revise our roadmaps, maintaining a development system that always looks 10 years into the future.
We believe automated driving, the IoT, and environmental impact reductions will be important themes. We strive to create innovation while working to build synergy between our future projections, the compactness and low energy consumption that are the strengths of our products, our new high-voltage ICs for medical products, and the like.
A research and development system that leverages our comprehensive strengths
In our vertically integrated business model, all the equipment and functions necessary for product development and supply, from circuit design to manufacturing and sales, are provided in-house. We carry out product development based on our roadmap to leverage these strengths using integrated development structures for each product line, encompassing everything from product planning to post-process design. For future core areas of product development, such as ultra-low power devices, ultra-low voltage devices, and sensors, we actively participate in joint industrial-academic collaborations, carrying out research and development that draws on cutting-edge findings and technologies.
Examples of innovation creation
Through our joint development with a university*1, we have released voltage-boosting circuits capable of operating with ultra-low power levels and ultra-low voltages. These ICs function with low voltages of just 0.35 V, making them optimal products in devices that boost and use the voltage obtained from low-voltage environment power generation elements, such as single or dual photovoltaic cells, thermal power generation elements, or plant power generation elements.
*1 Ritsumeikan University Douseki Laboratory
Quality Management and Quality Assurance
Based on our quality policy, we work to achieve even higher levels of quality. In particular, we combine the low-power-consumption, low-voltage, high-precision, and ultra-compact package technologies developed through years of wristwatch development and manufacturing in our distinctive product development, and manufacture highly reliable, high-quality CMOS IC*2 products. In order to meet our customers' demanding quality requirements, we use our integrated, in-house system to handle everything from circuit design to manufacturing and sales. Through this, we engage in quality assurance activities that precisely meet our customers' demands.
*2 “CMOS IC” is short for “Complementary Metal Oxide Semiconductor Integrated Circuit.”
CMOS ICs are integrated circuits that consume little power and suit for high integration.
Quality policy
Basic policy
We inspire and satisfy our customers with “Small, Smart, Simple” analog semiconductor products and solutions that make full use of our cutting-edge core technologies.
Activity policy
- We ensure conformance to the quality management system requirements, and implement continual improvements our quality management system using of process approach and risk-based thinking.
- We comply with statutes and regulations, and provide conforming products to customer requirements.
- We implement quality improvement activities to aim at zero field failures, and aim for the No.1 concerning the product quality of automotive components.
Quality management system
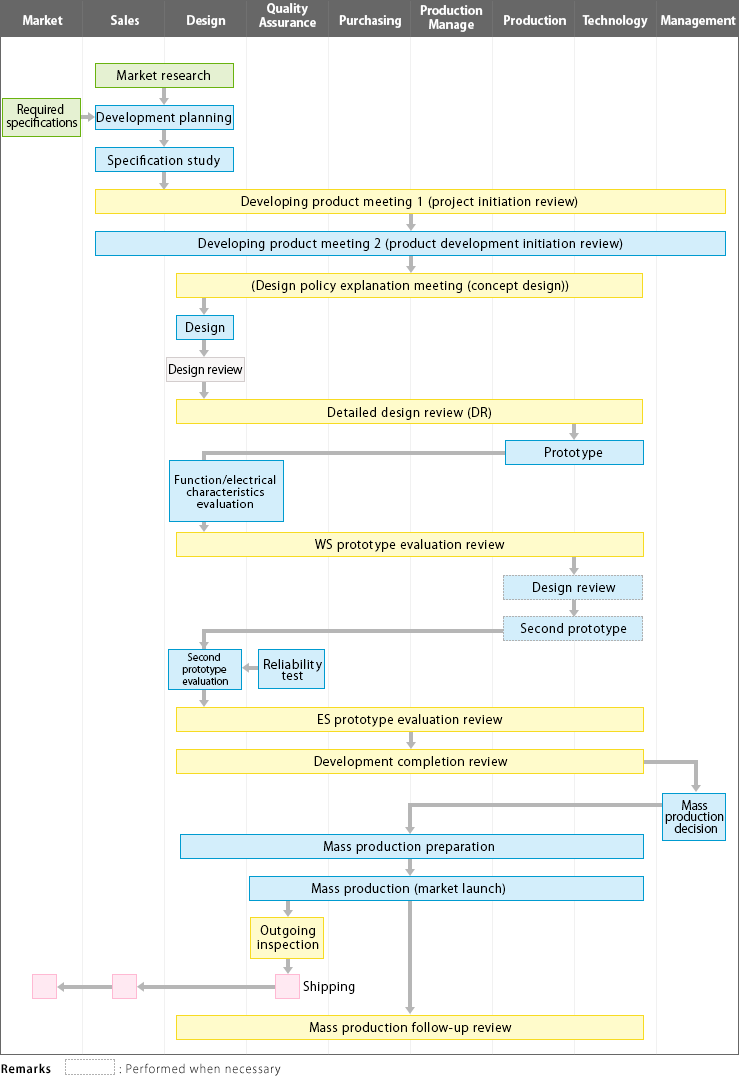
Attainment state of quality management system certification (FY2023)
We have attained certification under the international standard for quality management system ISO 9001:2015 (equivalent to JIS Q 9001:2015) and the automotive industry's international quality management system standard IATF 16949:2016.
For IATF 16949:2016, certification is attained separately for each of our plants.
- ISO 9001:2015 = JIS Q 9001:2015
ABLIC Inc.
Certificate No.:10000455546-MSC-UKAS-JPN - IATF16949:2016
ABLIC Inc.Takatsuka Unit
Certificate No.:10000455550-MSC-IATF-JPN
IATF Certificate No.:0435270
ABLIC Inc.Akita Unit
Certificate No.:10000483613-MSC-IATF-JPN
IATF Certificate No.:0435267
Quality improvement activities (1)
Quality Improvement Activities
We carries out quality improvement activities along three axes: Quality is improved through the training provided to production site operators; projects to aim at continual quality improvement and zero field failures activities are led by quality assurance and technical staff; and management members of all departments share defect information and deliberate on quality problem countermeasures in regularly held quality meetings.
Quality improvement activities (2)
Quality Training
We provide employees with quality training based on annual plans. Employees receive on-the-job training for each type of manufacturing process operation. We have defined rules that permit only approved employees to perform work, and these rules are scrupulously observed. We also actively support the acquisition of outside certifications. We currently have 1st grade and 2nd grade certified skilled professionals of semiconductor products manufacturing, as well as many other employees with legal certifications.
Quality improvement activities (3)
Ensuring Traceability
We have built a unique quality nonconforming report database that is integrated with our production management system. We use this database to record and retain detailed nonconforming records, analysis results, action plans, and the like. This database also contains the results of manufacturing process inspections and reviews by engineering departments. These can be used to create high quality, highly-competitive products by improving manufacturing processes and production yield based on analyses of past quality nonconforming records.
Customer Satisfaction
Customer satisfaction improvement activities
We pass all evaluation results regarding QCD* received from customers to all departments as feedback. After receiving the feedback, improvements are discussed across departments and implemented.
* QCD: Abbreviation for quality, cost, and delivery
Handling of quality issues
In the unlikely event of major quality issues in our products, related departments rapidly investigate and implement necessary countermeasures in accordance with our quality management system.
External incident response flowchart
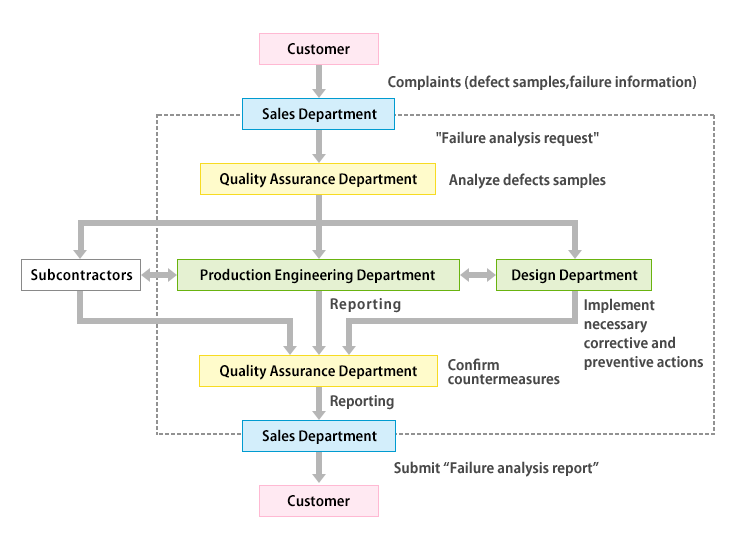